Design One, Build Many – why it could be set for take-off
Jugal Mehta, our Deputy Process Manager, explores the potential of design one, build many and what it will take to make this strategy a scalable solution in the energy sector.
Design One, Build Many – or D1BM – is not a new concept. It’s been discussed in the energy services business for decades. Yet it’s never really materialised at scale. At Petrofac, we believe that could be about to change – because D1BM lends itself perfectly to the challenge of delivering energy transition projects at the pace and scale needed. The learnings can be implemented across many other project types too.
Defining D1BM
D1BM refers to a strategy that involves the design of a standard set of components that can be replicated across multiple projects. The automotive industry provides a perfect example of a successful D1BM implementation, with car manufacturers standardising components like engines, transmissions, and electrical systems across various models.
Similarly, the approach has also been adopted by some of the Engineering Procurement and Construction (EPC) players in the energy industry. Here, there have been some pockets of success, for example, the delivery of standardised wellheads across marginal oil and gas fields. But, in a complex and risk-averse sector like energy, most clients have demanded bespoke designs for site-specific assets and client-specific standards.
At Petrofac, we believe this is about to change. D1BM may never be relevant for all project types. But it is becoming increasingly relevant for many of them, especially in the energy transition world.
D1BM has three key benefits – which, in combination, translate to a fourth powerful advantage
The first benefit is in cost savings. If a set of components can be standardised, the EPC firm avoids the need to start afresh with every new project, bringing a significant scale efficiencies and cost reductions to the engineering phase.
Second, there are considerable efficiency improvements. Procurement is faster, supply chain partners find it easier to plan and invest in the standardisation of components, inventory management is simpler, and the scope for modularisation brings further efficiencies. Meanwhile, with a familiar design, project execution becomes far smoother, more predictable, and quicker.
Third, we have the impact on quality. When a design is used on multiple projects, the experience from the previous executions is carried over to all subsequent projects, liberating the potential for higher quality standards and incremental improvements.
In combination, these benefits add to the environmental sustainability of any project. At a time when every major player in the industry has decarbonisation objectives to meet, this can become a powerful advantage.
Many energy transition projects lend themselves to D1BM
D1BM is particularly suited to many energy transition projects, such as solar plants or wind farms, where repeatability is key. Typically, these assets are comprised of a series of highly replicable components, like wind turbines, solar panels, power packs and grid interconnections.
In the case of an offshore windfarm, for example, a single platform can be designed for the base case, covering all the anticipated requirements within the same vicinity. And an alternative platform can then be provided with a base case plus additional platform-specific requirements such as changes in water depth for the jacket design. The same approach can also be followed in green hydrogen facilities, where there is a very strong rationale for standardisation and modularisation. EPC firms can create project designs that are highly adaptable and customisable by breaking down standard components into smaller, interchangeable, standardised modules. Then, if design requirements change from project to project, one module can be swapped out for an alternative, rather than having to re-plan the entire facility. Modules can also be built offsite, reducing construction timescales. Then, during operations, maintenance programmes can focus on and isolate specific modules.
In essence, the core benefit is that D1BM techniques can help the wider industry to deliver energy transition projects at the speed and scale that’s now required – and to do so in a way that brings far more efficiency and sustainability than has previously been possible.
D1BM learnings can be applied right across the energy sector
As the energy industry gains more experience of D1BM and the benefits it brings, the learnings can also be applied, at scale, to the world of hydrocarbons.
In the past, D1BM concepts have been used across some oil and gas fields which share similar characteristics. But there is definitely scope to extend the approach. Standardisation could be applied to more platform designs. Similarly, the type of segmentation we see in most pipeline system – such as manifolds, flowlines, and trunkline metallurgy – lends itself to more standardisation and modularisation.
Looking further downstream, there are clear opportunities to standardise the key components of some refineries based on both the final product and the nature of the feedstocks. At its root, every refinery is made up of a series of process units – such as crude distillation units – storage tanks and enabling utilities. So, again, there is potential for far more standardisation and modularisation.
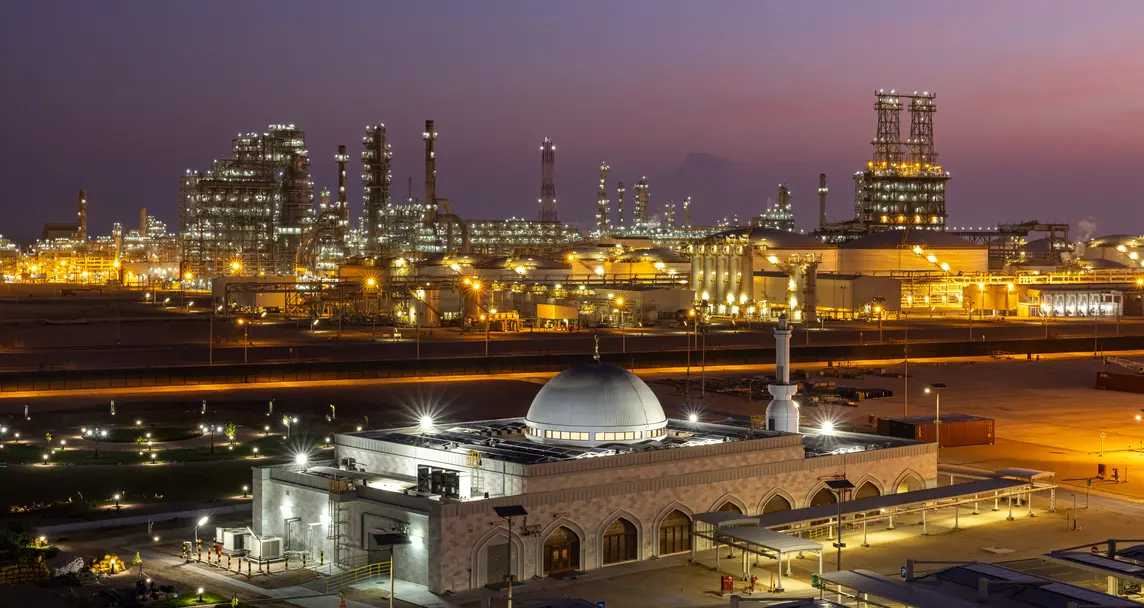
Duqm Refinery, Oman
Why D1BM isn’t a one size fits all solution
Of course, D1BM won’t be right for every project, and there will always be some challenges and limitations to work around.
By its very nature, D1BM limits flexibility and restricts customisation options. So, for clients who need a site-specific solution, it won’t be appropriate. But even with the most bespoke of designs, there may still be an opportunity to select from a menu of modularised components – such as the associated pipeline systems, or certain process units.
D1BM can also increase supply chain risks. Many of the concept’s benefits come from repeatable operations, shared learnings, and accumulated knowledge. This can bring a dependency on a relatively small number of suppliers. The approach to supplier management and contracting therefore needs to evolve, with more of an emphasis placed on long-term strategic partnerships and aligning goals.
At a time when technology is quickly evolving, D1BM can also mean that standard designs become quickly outdated. Part of the design challenge, therefore, is to anticipate forthcoming technological changes. Designers may need to look for ways to enable forward compatibility – perhaps in the way they think about modularisation.
Aiming for the best of all worlds – standardisation and flexibility and continuous improvement
In summary, a balanced approach is needed. D1BM brings all the benefits of standardisation, enhanced quality, and scale economies. But it also needs to accommodate flexibility, enable continuous improvement, and anticipate tomorrow’s innovations. To succeed, all parties – including EPC firms, clients, suppliers and process vendors – need to evolve the way they approach planning and contracting. For all of us, the focus needs to be on mid-to-long-term benefits, not just short-term project delivery.