We build the boxes that power the world
In the vast expanse of the ocean, where the ceaseless power of wind reigns supreme, an engineering marvel emerges: a ‘big yellow box’. These colossal offshore wind transmission assets stand ready to harness the raw power of nature.
If we are to meet our 2030 renewable energy targets, which for the United Kingdom requires a fivefold increase in current offshore wind capacity (to 50GW) and, for Europe an increase of at least 25 times the current capacity, we need to step up the race to deliver the infrastructure needed to achieve this. This includes the imposing structures tucked in between offshore wind turbines and visible from our shores – the ‘big yellow boxes’
In this article, we unpack the facts about this vital part of the wind energy delivery chain.
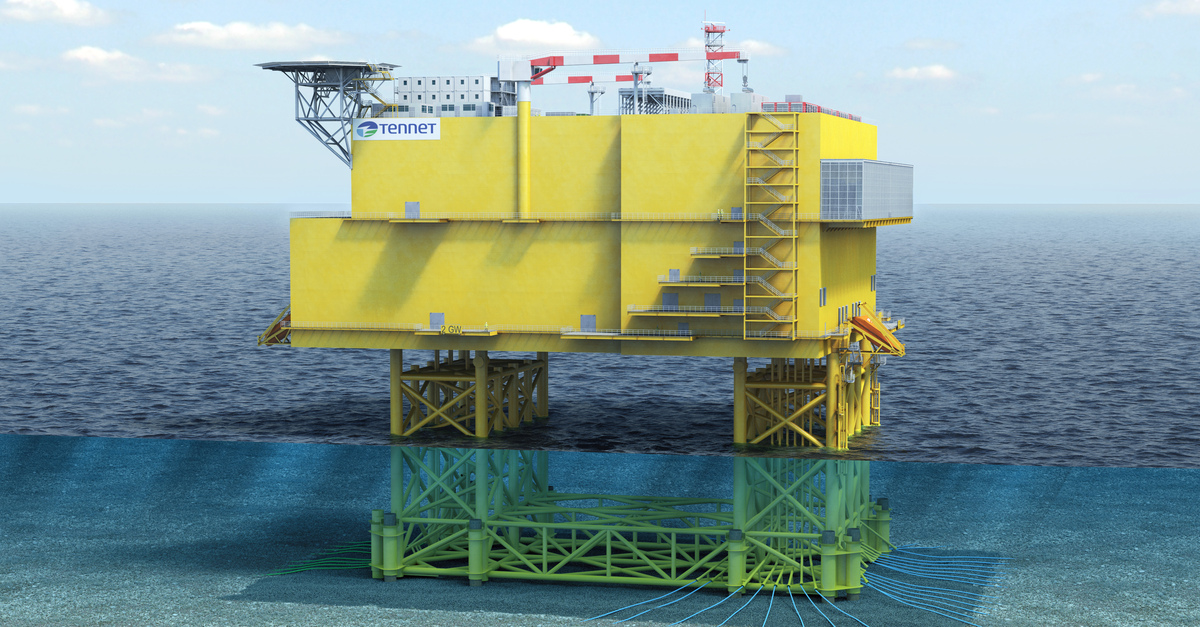
Petrofac and Hitachi Energy have been awarded a multi-year Framework Agreement by TenneT as it works to expand offshore wind capacity in the Dutch-German North Sea
What are the boxes?
Though not always boxes (some are open frame), nor always yellow, these structures sat amongst offshore wind turbines are substations or transmission assets. They house the transformers, switchgear, and other electrical equipment needed to convert the electricity generated by turbines into a current that can be reliably carried to shore by subsea cables.
HVAC or HVDC?
Turbines generate electricity in the form of high-voltage alternating current (HVAC). But transporting this power efficiently to shore can result in fluctuation and loss depending on how far the wind farm is from land. If a wind farm is within approximately 50 kilometres of land, the subsea cables can effectively carry the power as alternating current (AC). But for distances typically beyond 70 kilometres, the AC current received from the turbines needs to be converted into direct high-voltage current (HVDC) to transport via cable without significant fluctuation and loss.
Withstanding the elements
The reliability of this electrical equipment is vital for maintaining a steady flow of electricity from the farm to the grid. This means the offshore structures bearing this equipment must be wave, wind, current and even earthquake resistant.
Most support structures comprise steel plates, tubes and beams painted for corrosion protection. The containers housing the electrical equipment are made from carbon steel, typically coated in corrosion-resistant layers of paint. The jacket (the legs and bracing) or monopile support structures (single legs) submerged in water are treated with other, more robust corrosion-resistant technologies, such as sacrificial anodes (that’s a story for another time).
Illuminating structures
The question beckons: “why are substations, or transmission assets, yellow?” Yellow, orange, red, black, and white are aposematic: a colouration that denotes warning. They are also easily visible in the environment, even in low light. In nature, birds, bees, frogs, and snakes use yellow as a warning to potential threats and predators. Over time, these warning colours have been reflected in our manufactured environment. In an offshore environment, the use of yellow ensures structures are visible, aiding marine navigation. In practice, this is only the parts visible from the waterline (lowest point to accommodate low tides) and above.
Design considerations
Where water depths used to be a limitation for the wind turbines themselves, advancements in design and technology mean wind farms are now being built in much deeper waters – with turbines supported on floating substructures. In theory, fixed bottom substations have always been able to handle much deeper waters, with depths as great as those seen for offshore oil and gas facilities; these can be as deep as 500m, more than the height of the Petronas Towers in Kuala Lumpur, Malaysia. Today, design and development are underway to allow offshore substations to be floating structures, too, meaning the future's offshore wind farm developments may be in places we could never have reached before.
One size fits all?
While there is no optimum shape or size for these offshore structures, the capacity needed for the wind farm dictates what equipment and how much of it goes onto the platform. There is almost a bespoke design every time. That is something those collaborating on TenneT's 2GW projects, including Petrofac, aim to change. One of TenneT's key project objectives for the 2GW Programme is developing a more standardised, repeatable design: this offers opportunities for a more efficient design approach and a solution to delivering the significant number of 'big yellow boxes' needed to reach government goals faster. The race is indeed on.